
Marija Jankovic, ROHM Semiconductor GmbH,Germany
Marija Jankovic obtained BSc and MSc in electrical engineering at University of Belgrade, Serbia in 2010 and 2011, respectively. She obtained a PhD degree in power electronics at University of Nottingham, UK. Her research focuses on grid-tied converters and control strategies. In 2017, she joined Porsche engineering Services GmbH as a development engineer of high-power charging stations for Electric vehicles. In 2020, she joined ROHM Semiconductor as part of the technical customer support team, dealing with SiC MOSFETs as a key product and automotive applications, such as traction inverter and On-board charger.
Keynote Title: Semiconductors are shaping automotive applications
Abstract: Electrification of the vehicles has been a trend in the last two decades and the number of hybrid and full electric vehicles on the streets is significantly increasing. As a result, a significant research and development has been done not only on electrical motor development and battery technology development, but also on semiconductors responsible for energy conversion within the car. High efficiency and high power density / low weight requirements cannot be achieved with silicon semiconductors and are therefore addressed with wide bandgap semiconductors such as silicon carbide (SiC) and gallium nitride. SiC products are successfully addressing many automotive applications thanks to their fast switching capability, low static losses and high breakdown voltage suitable for high battery voltage applications. On the other hand, some applications are still addressed with silicon products such as IGBTs due to the lower cost and slow switching. This talk will cover the trends in the modern automotive applications from a perspective of semiconductors selection.

Stefano Fiorati is Director of Innovation & Advanced Propulsion Systems, CNH, Italy.
Stefano Fiorati is responsible for expanding alternative fuels, electrification and driveline technologies across the Company’s entire agriculture and construction product portfolio. Prior to this appointment, Mr. Fiorati was Manager of Tractor Innovation, Zero Emission & Advanced Drivetrain at CNH from 2021-2023 and Tractor Innovation from 2014-2021. In this previous role, he was technical project leader for the New Holland T6.140 Methane Powered tractor prototype and subsequent concepts, presented in 2015 and 2017 respectively. Mr. Fiorati started his professional career with CNH Industrial in 2011 as Mechanical Design Engineer within the Innovation department. Stefano Fiorati has a PhD in Mechanics of Machine awarded jointly by the University of Ferrara, Italy, and the Katholieke Universiteit Leuven, Belgium. He has a master’s degree in Mechanical Engineering from the University of Ferrara, Italy.
Keynote Title: Modeling and development of electrified powertrain in off-highway vehicles
Abstract: In agriculture, alongside food production, the pursuit of efficiency and sustainability has emerged as a top priority. To achieve the Paris climate protection goals by 2050, comprehensive measures to reduce CO2 emissions are required. With the world’s growing population, the demand for increased food production combined with the need to reduce the environmental footprint of agricultural production has never been more important. In the area of agricultural machinery development, these machines are traditionally powered by diesel engines, which may well change in the future. Alternative and new drive solutions range from electric and hybrid technologies to bio and synthetic fuels and hydrogen technologies could revolutionize the agricultural machinery sector. The introduction of cutting-edge innovations should not only increase performance, but also reduce greenhouse gas emissions and strengthen operational sustainability. The technologies currently being investigated and that will be investigated need to be explored through a deep data analysis in conjunction with simulations to cover key aspects from the most common related to packaging to the ones like performances, cooling, battery sizing and control strategies development. This with the goal of reducing more and more the development time while keeping cost under control to achieve a “Sustainable” development.

Giovanni Puccetti, Electric Motor Project Engineer – Ducati Motor Holding, Italy
Giovanni Puccetti was born in Lugo (RA) in 1986. He attended the Electrical Engineer of Alma Mater Studiorum, University of Bologna, where he received the degree and Ph.D. degree in 2011 and 2014, respectively. Since 2015 he worked in Magneti Marelli as electric motor designer for Electric & Hybrid vehicles, in R&D department. Since 2018 he worked in Bonfiglioli Riduttori as industrial motor & HEV drives design engineer and as electric motor design manager for the same company. Since July 2024 he has been working as Electric Motor Project Engineer, joined with eMobility team at Ducati Motor Holding.
Keynote Title: Electric racing motorcycle: current status and trends
Abstract: Status of art of the electric racing bike will be presented with particular focus on Ducati V21L MotoE Project. Technical details, performances and characteristics will be shown. Finally, the future and the challenge of the electrification from Ducati point of view will be discussed.

Matias Troncoso, Ferrari SpA
Matias Troncoso: Born in Chile in 1988, received PhD and MSc in electrical engineering from Politecnico di Torino, Turin, Italy in 2024 and 2013 respectively. Currently the assembly and testing manager of the electromechanical components in Ferrari, has been involved from the very beginning of the hybrid / electric era in Ferrari, working in the development of the LaFerrari, SF90 Stradale, 296 GTB, among others.

Irene Donà, Ferrari SpA
Irene Donà achieved her Master Degree in Materials Engineering at Padova University in 2010.
From 2010 to 2017 Test Engineer for Fiamm group, working with different battery chemistries (Nickel – Sodium, Lead acid and Li-Ion), technologies (from prototyping to production) and applications (stationary, railway, automotive and energy storage).
Since 2017 part of Ferrari Hybrid Development team, currently as Battery Testing Manager dealing with performance, endurance, safety and homologation tests for battery and its subcomponents.
Keynote Title: Testing of high performance electric powertrain components: challenges and solutions
Abstract: The validation of electric powertrain components is often overlooked during early engineering studies, despite its critical role in ensuring the reliability and safety of electric vehicles. This talk addresses the challenges and solutions surrounding the testing of key components such as batteries, inverters, and electrical machines. On one side, the specific component must be tested to verify that the functional and reliability specifications defined during the design phase are met. On the other side, the design has to be developed within homologation standards, such as R100 for safety requirements in Europe or GBT 18488 for electrical machines in China. These standards dictate rigorous testing requirements on environmental conditions or safety obligations that the components have to meet. To overcome these challenges robust testing campaigns are conducted throughout the component’s development, on specific test benches. Often, for high-performance powertrain components, these test benches are tailor-made for the components specifications and allow continuous monitoring of the component state. By addressing the challenges in validating high-performance electric powertrain components and implementing effective testing solutions, manufacturers can ensure the quality and safety of electric vehicles, fostering widespread adoption and driving the transition towards sustainable transportation.

Michele Bolpagni, Aqua superPower Limited, Italy
Michele graduated with a degree in Mechanical Engineering from Politecnico di Milano and has spent his subsequent career in the e-Mobility field. After spending few years in developing AC and DC charging infrastructure, he joined Aqua superPower in 2021 as Product Manager and Country Manager Italy. He is in charge of developing the business in Italy, South of France and Central Europe, as well as working together with the Deployment department.
Keynote Title: A global network of charging infrastructures for electric boats
Abstract: Aqua superPower is the first fully marinised dockside network of fast chargers for electric boats. The product range includes AC and DC charging solutions with a maximum power of 350 kW, allowing DC compatible powerboats to rapidly recharge and extend their autonomy. Aqua superPower has developed the first supercharger specifically engineered and rated for use in marine environments. Built to IP65 standards, Aqua superPower is a revolutionary and sustainable marine charging solution. There are currently over 30 million recreational boats in the world. Assuming the boat market continues to grow in line with historical trends, it is likely there will be more than 1 million electric boats by 2030. Regulation will accelerate this trend and more and more areas will only be accessible to electric boats. www.aqua-superpower.com

Giuseppe Esposito Corcione, CEO & Founder REINOVA S.p.A., Italy
Born in 1979. Mechanical engineer.
Fueled by Curiosity, Innovation and Passion for Technology.
Dreamer. Entrepreneur. Disseminator for the mobility of the future.
Nominated as one of the 100 Italian excellences 2022 with the mention for innovative and sustainable mobility. 2 wonderful children, Luca and Andrea. I love music and play the drums Motors, cars, sports cars, F1 and racing are my passion and my world! Thinking outside the box, finding ideas and solutions are my natural place to be.
Innovating towards sustainable, connected, shared and safe mobility is my mission. I develop electronic components such as batteries, electric motor, E-axl, winding technologies, electronic components. My rational approach and my thinking are constantly fueled by the desire to discover and know the world in its completeness and totality, since I believe that only with an overall vision can detail be best evaluated and managed. And only by having a perfect knowledge of the details can we build a winning strategy. My work is my passion and my passion is my work.
Keynote Title: From Automotive to Compumotive: the new challenges of electrification and the evolution of mobility to 2050

Francesco Papini, Ansys Italia srl
Dr. Francesco Papini joined Ansys in 2023 as a Senior Application Engineer, focusing on thermal and electromagnetic analysis of electric machines. E-machine design and analysis has been the core of Francesco’s professional activities for the last 15 years. After gaining his PhD from the University of Pisa in 2010, he joined the GE Global Research Centre in Munich, Germany, where he was involved in all kinds of applications, from multi MW wind turbines to fractional-HP refrigerator compressors. In 2018 he moved to the Italian automotive industry, first with Eldor Corporation and then with Marelli e-Powertrain, designing electric propulsion motors for hybrid and battery electric vehicles as well as other e-mobility solutions.
Keynote Title: E-machine Design, Analysis and Optimization with Ansys
Abstract: The trend of electrification of transportation is getting momentum, with increasing applications of electrical machines and drives not only for cars and light commercial vehicles, hybrid or full electric, but also for heavy duty or off-road vehicles such as in the agricultural or construction sectors. However, to increase the share of green transportation and achieve our decarbonization goals, the cost and development time of electric drive-trains must go down. Looking at the electrical machine component, such effort is often hindered by the fact that e-motor-design is a multi-physics endeavour with electro-magnetic, thermal and mechanical engineers interacting in all stages of the motor development cycle.
This talk will focus on how Ansys can speed up the development cycle and the optimization of the e-motor. More particularly, Motor-CAD is our multi-physics design tool dedicated to electrical machines, allowing the single engineer to perform all calculations in each of the physical domains within a single software and without needing to pass data, reconstruct models and setup simulation in different environments. Furthermore, 20+ years of engineering experience and continuous development are poured into the software, helping the designer to make decisions also on aspects they are less familiar with.
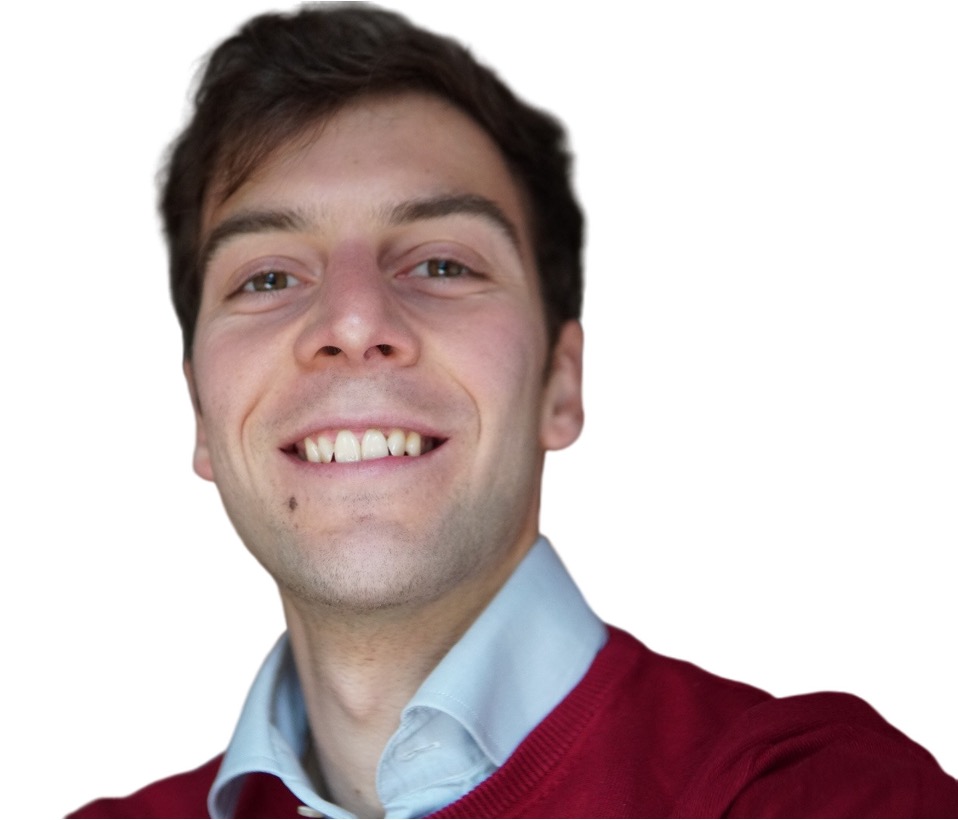
Michele Merelli, Particleworks Europe / EnginSoft
Michele joined EnginSoft in 2019, after an internship in ABB. He achieved his Master Degree in The Netherlands (Rijksuniversiteit, Groningen), after a Bachelor in Materials and Nanotechnology Engineering in Italy (Politecnico di Milano, Milan). He focused on simulations with Moving Particle Simulation ever since joining EnginSoft, specializing in e-motor cooling and thermal management simulations, supporting several companies with remote assistance and onsite visits across Europe. Currently, he is Project Engineer in EnginSoft and Pre- and Post- Sale Manager for the Moving Particle Simulation software Particleworks in Europe.
Keynote Title: Better cooling and lubrication of e-Drives with Moving Particle Simulation
Abstract: Particleworks, a popular mesh-less simulation tool for Computational Fluid Dynamics (CFD) widely used in the automotive industry. The novelty of the methodology is the integration of the fluid and thermal simulations in one, mesh-less and easy to setup digital model. This approach proved to be particular efficient in dealing with the simulation of oil jets directly cooling the coils, a strategy that proved to be superior to external, stator-based water jackets. The approach is able to provide airflow estimation, churning losses due to oil on gears, airgap contamination evaluation and Heat Transfer Coefficient estimation due to the multi-phase flow.
Moreover, by integrating a thermal solver, Particleworks offers a comprehensive approach from e-motor design to thermal management working with the same CAD and simulation interface.
Finally, after discussing the benefits and the features of the approach, we will discuss recent demonstrations of industrial examples and experimental validations of e-motor cooling and e-drive lubrication.

Jovan Zelic, Typhoon HIL, Serbia
Jovan Zelic has been part of Typhoon HIL since 2019 and is a Senior Member of the Modeling Team. He holds a Master’s degree in Electrical and Computer Engineering from the Faculty of Technical Sciences in Novi Sad, Serbia, with emphasis on power electronics and electric machines. His areas of interest include electric drives and battery chargers of electric vehicle batteries.
Hardware-in-the-Loop (HIL) for development and testing of electric motor drive control software
The shift from hardware-defined to software-defined vehicles is progressing rapidly marked by the adoption of electric motors for propulsion in lieu of internal combustion engines. Electric vehicle propulsion essentially operates on a variable-speed electric drive system. This requires new approaches for developing and testing control software, with primary components being the electric machine and an inverter. Given the longstanding presence of variable-speed motor drives in the industry, certain development and testing methodologies can be leveraged from industrial drives to the automotive sector. Hardware-in-the-Loop (HIL) methodology has been widely used for testing of power electronics controls. This demo session will showcase Controller Hardware-in-the-Loop (C-HIL) methodology, where a real controller is connected to a real-time HIL simulator which replicates the power stage of the electric drive. The C-HIL environment enables rapid and safe testing of control algorithms in a environment setting, mitigating the heightened safety concerns and procedural complexity typically associated in laboratory testing.